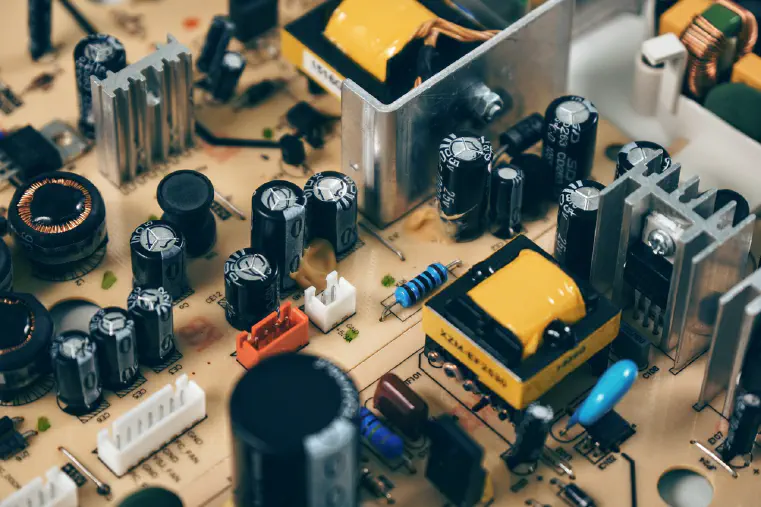
Unveiling Mechanisms: How to Test a Capacitor
Understanding the Capacitor
A capacitor is an electronic component that stores and releases electrical energy.
It is a passive device consisting of two conductive plates separated by an insulating material known as a dielectric.
When a voltage is applied across the plates, electrons accumulate on one plate and deplete from the other, creating an electric field between them.
This accumulation of charge builds up a potential difference, or voltage, across the capacitor.
The amount of charge that a capacitor can store depends on its capacitance, which is determined by the surface area of the plates, the distance between them, and the characteristics of the dielectric material.
Capacitors are used in a wide range of electronic circuits, such as power supplies, filters, timing circuits, and motor starting circuits, to name a few.
They play a crucial role in stabilizing voltage levels, smoothing out fluctuations, and storing energy for short bursts when needed.
Why Do Capacitors Need Testing?
Capacitors are fundamental components in electronic circuits, and ensuring their proper functioning is crucial for optimal system performance.
There are several reasons why capacitors need to be tested.
Firstly, performance checks are necessary to evaluate the effectiveness of capacitors within a circuit.
This involves measuring parameters such as capacitance, leakage current, and equivalent series resistance (ESR).
By conducting these tests, any variations or abnormalities in the capacitor’s electrical properties can be detected, indicating potential issues that may affect the overall performance of the circuit.
Secondly, capacitors may also require testing for fault diagnostics purposes.
In case of capacitor failures, such as short circuits or open circuits, testing can help identify the faulty component and facilitate timely repairs or replacements.
This not only helps in minimizing system downtime but also prevents further damage to other components.
Lastly, preventive measures dictate that capacitors should be periodically tested to proactively identify any signs of degradation or aging.
With time, capacitors can experience a decrease in performance or even fail completely, which can lead to system malfunctions or failures.
By regularly testing capacitors, their condition can be assessed, allowing for timely maintenance or replacement to avoid potential problems.
In conclusion, testing capacitors is essential for performance evaluation, fault diagnostics, and preventive maintenance, ensuring the reliability and longevity of electronic systems.
How to Test a Capacitor?
Testing a capacitor is an essential step in any electronic troubleshooting process.
Whether you’re a professional technician or a DIY enthusiast, knowing how to test a capacitor can save you time and money.
There are several methods you can use to test a capacitor, and in this article, we will guide you through the step-by-step process.The
first method involves using a multimeter, which is a versatile tool that can measure various electrical properties.
To test a capacitor using a multimeter, start by disconnecting the capacitor from any power source and discharging it completely.
Then, set your multimeter to the capacitance mode and connect the positive and negative leads to the respective terminals of the capacitor.
The multimeter will display the capacitance value, indicating whether the capacitor is functioning within its rated capacitance.Another
method involves using an analog meter, which uses a needle to indicate the measurements.
Similar to multimeter testing, you will need to disconnect and discharge the capacitor.
Set your analog meter to the capacitance range and connect the leads to the capacitor terminals.
The needle will move to a certain value, indicating the capacitance of the capacitor.In
addition to electrical testing, it’s also important to inspect the capacitor for any signs of physical damage.
Look for bulging or leaking capacitors, as these are common indicators of failure.
Other physical damages include burnt marks, discoloration, or a swollen appearance.
If you notice any of these signs, it’s likely that the capacitor needs to be replaced.In
conclusion, testing a capacitor is a straightforward process that can be done using various methods.
Whether you use a multimeter or an analog meter, make sure to disconnect and discharge the capacitor before testing.
Additionally, inspecting the capacitor for physical damage is equally important to ensure the overall functionality and safety of your electronic devices.
Conclusion
Testing capacitors is a crucial step in ensuring the proper functioning of electronic devices.
Capacitors play a vital role in various circuits by storing and releasing electrical energy.
However, over time, capacitors can degrade or fail, leading to malfunctions or even complete device failure.
Therefore, it is essential to test capacitors regularly to identify any potential issues and prevent future problems.
To test a capacitor safely and successfully, there are several key steps to follow.First,
before conducting any tests, it is crucial to ensure your safety by turning off the electronic device and disconnecting it from any power source.
Capacitors can store electric charges, which can be dangerous if mishandled.
Always remember to discharge the capacitor completely before proceeding with any tests.
This can be done by using a resistor or shorting the capacitor’s terminals with suitable precautions.Once
the capacitor is discharged, you can proceed with the actual testing.
There are various methods to test capacitors, depending on the equipment available and the specific requirements.
One common method is to use a multimeter.
Set the multimeter to the capacitance measurement mode and carefully connect its probes to the terminals of the capacitor.
The multimeter will display the capacitance value, allowing you to verify if it falls within the expected range.Another
testing method utilizes an ESR meter, which measures the equivalent series resistance of the capacitor.
High ESR values indicate a faulty or degraded capacitor.
By comparing the measured ESR with the manufacturer’s specifications, you can determine the health of the capacitor.Furthermore,
visual inspection is also essential in identifying any physical damages or abnormalities in the capacitor.
Look for bulging, leaking, or exploded capacitors, which are clear signs of failure and require immediate replacement.In
conclusion, testing capacitors is of utmost importance to ensure the reliable performance and longevity of electronic devices.
By following the necessary steps and using appropriate testing methods, you can identify faulty or degraded capacitors and take the necessary action.
Regular testing and maintenance will help prevent unexpected failures, save costs on repairs, and maintain the overall functionality of your electronic devices.
FAQs
What is a capacitor?
A capacitor is an electronic component that stores and releases electrical energy.
It consists of two conductive plates separated by a dielectric material.
Why is it important to test a capacitor?
Testing a capacitor is important to ensure its proper functioning and performance.
It helps identify faulty or damaged capacitors, which can cause electrical failures or malfunctions in electronic devices.
By testing capacitors, potential risks such as short circuits, voltage leaks, and excessive heat generation can be minimized, preventing potential damage to the circuit or device they are a part of.
What are the methods for testing a capacitor?
There are several methods for testing a capacitor.
These include using a multimeter, performing a capacitance test, checking for visual signs of damage or leakage, using an ESR meter, and employing an oscilloscope to analyze waveform patterns.
What tools are needed to test a capacitor?
To test a capacitor, you will need a multimeter with capacitance measurement capabilities.
Additionally, a pair of test leads or probes is required to connect the capacitor to the multimeter.
What should be considered before testing a capacitor?
Before testing a capacitor, it is important to consider the voltage rating of the capacitor to ensure it is compatible with the testing equipment and circuit.
Additionally, the capacitance value of the capacitor should be known in order to compare the actual value with the expected value during testing.
Lastly, the capacitor should be discharged to prevent any potential safety hazards or damage to the testing equipment.
How to interpret the results of a capacitor test?
Interpreting the results of a capacitor test involves analyzing the measurements and comparing them to the expected values.
If the measured capacitance closely matches the nominal value, then the capacitor is likely in good condition.
However, if the measured capacitance deviates significantly from the expected value, it suggests that the capacitor may be faulty or have deteriorated.
Other factors such as leakage current, equivalent series resistance, and frequency response should also be taken into consideration when interpreting the test results.
What are the signs of a faulty capacitor?
Some signs of a faulty capacitor include bulging or leaking, a burning smell, electrolyte leakage, electrolyte corrosion, and failure to start or run electronic devices.
Can a damaged capacitor be repaired?
No, a damaged capacitor cannot be repaired.
When a capacitor is damaged, it is not possible to fix it back to its original working condition.
It is recommended to replace the damaged capacitor with a new one to ensure proper functioning of the electrical circuit.
What precautions should be taken while testing a capacitor?
When testing a capacitor, it is important to take certain precautions to ensure safety and accuracy of the results.
Firstly, always make sure to discharge the capacitor before testing to prevent any electrical shocks.
This can be done by short-circuiting the capacitor terminals with a resistor or wearing appropriate safety gloves.
Secondly, check the voltage rating and capacitance value of the capacitor to ensure it is within the range of your testing equipment.
Using higher voltage or exceeding the capacitance limit can lead to damage.
Finally, handle the capacitor with care and avoid touching the leads while conducting the test to prevent any interference or accidental connections.
Is it possible to test a capacitor without removing it from the circuit?
Yes, it is possible to test a capacitor without removing it from the circuit.
Various methods such as voltage tests, resistance tests, and capacitance tests can be used to determine the functionality and health of a capacitor while it is still connected in a circuit.
What are the potential risks involved in testing a capacitor?
Testing a capacitor without proper precautions can be dangerous.
The capacitor may still be charged with high voltage even after it has been disconnected from the power source.
Touching the terminals or components of a charged capacitor can result in electrical shock or burns.
Additionally, if the capacitor is faulty or damaged, it may explode or rupture during testing, causing injury or property damage.
It is essential to discharge the capacitor and follow safety measures to minimize the risks involved in testing.
What are the common mistakes to avoid while testing a capacitor?
Some common mistakes to avoid while testing a capacitor include incorrect polarity connections, using the wrong testing equipment or settings, failing to discharge the capacitor before testing, and not taking proper safety precautions.
How frequently should a capacitor be tested?
The frequency at which a capacitor should be tested depends on several factors, including its usage, operating conditions, and the specific industry requirements.
In general, it is recommended to test capacitors periodically, at least once a year, to ensure their proper functioning and to detect any potential issues or deterioration over time.
However, in certain critical applications or environments with harsh conditions, more frequent testing may be necessary to ensure the reliability and safety of the capacitor.
Can all types of capacitors be tested in the same way?
No, not all types of capacitors can be tested in the same way.
Different types of capacitors have different construction, materials and properties, which require specific testing methods.
For example, electrolytic capacitors need to be tested for leakage current and capacitance, while ceramic capacitors require testing for capacitance and temperature stability.
It is important to refer to the manufacturer’s guidelines or datasheet for each specific type of capacitor to ensure the correct testing procedures are followed.
Is professional assistance necessary for testing a capacitor?
Professional assistance is not always necessary for testing a capacitor.
With the right tools and knowledge, it is possible to test a capacitor on your own.
However, if you are uncertain or lack experience in handling electrical components, seeking professional assistance is highly recommended to ensure accurate and safe testing.